有色冶金烟尘处理与资源化技术
随着环保要求的不断提高和处理工艺的不断改善,铜烟尘的综合利用方法逐渐从传统火法处理工艺向湿法处理工艺发展,全湿法工艺、湿法一火法联合工艺和选冶联合工艺等方法得到了广泛的应用。
(1)火法处理铜烟尘
20世纪60年代初,主要采用全火法流程回收铜烟尘中的锌、铅,其他有价元素未得到有效回收利用。传统全火法处理铜烟尘的工艺主要有反射炉熔炼、电弧炉熔炼、鼓风炉熔炼及直接回炉熔炼等,其中采用较多的是鼓风炉熔炼,主要流程为:铜烟尘先经鼓风炉还原熔炼得出铅铋合金,铅铋合金经处理后浇铸成阳极进行电解,析出的铅经碱性精炼后铸成电铅锭;铋残存于阳极泥中,再熔化并除铜,加碱熔铸则得到粗铋和含铜残渣。粗铋经碱法除锑、加锌除银、氯化除铅锌,最终精炼后得到精铋。银锌渣用来回收银,氯化锌渣生产氯化锌,氯化铅渣回收铅。该工艺优点在于处理量大、成本较低、铅和铋回收率高(回收率分别可达90%和80%),缺点是操作环境差、会产生二次污染,且没有对烟尘中其他有价元素进行有效回收。
(2)全湿法工艺处理铜烟尘
火法处理铜烟尘存在着回收率低,操作环境较差,会产生二次污染等问题,因此,湿法冶金技术逐渐在铜烟尘的综合利用上得到了应用。全湿法工艺处理铜烟尘的基本流程为“浸出一置换沉铜一氧化中和除铁—浓缩结晶”生产硫酸锌,浸出渣则用于生产三盐基硫酸铅。
酸浸——碳酸铵转化法是全湿法工艺回收铜烟尘中的有价元素。将铜烟尘酸浸之后,浸出液采用置换沉铜—氧化除铁—浓缩结晶生产硫酸锌有效的回收浸出液中的铜、锌,并采用P204做萃取剂回收浸出液中的铟。铅以硫酸铅形式存在于浸出渣中,渣中同时还含有铋,故先对浸出渣进行铅、铋分离,再采用碳酸铵转化一硝酸溶解——硫酸沉铅的转化法生产三盐基硫酸铅。首先将浸出渣水洗去酸后,在常温常压下加碳酸铵使硫酸铅转化为碳酸铅,其后加硝酸将碳酸铅溶解,固液分离后,浸出液再次使用硫酸沉铅生产三盐基硫酸铅,铅的回收率可达到75%以上,浸出渣中的铋得到有效富集和回收。
水浸——氯化浸出的全湿法工艺回收铜烟尘中的铜、铅、银、锌。将烟尘进行水浸后,浸出液采用置换沉铜一中和除杂—浓缩结晶生产硫酸锌的工艺回收铜、锌,浸出渣用CaCl2-NaCl溶液加热常压浸出,将渣中的铅浸出生产三盐基硫酸铅。经氯化浸出后,铅以氯化铅形式结晶析出,银以海绵银形式被置换回收。结晶析出的氯化铅水洗去残留Cl~后,加入硫酸,在80℃下充分搅拌使氯化铅转化为硫酸铅,再将硫酸铅水洗至中性,缓慢加入NaOH溶液生产三盐基硫酸铅。全湿法处理铜烟尘工艺具有污染小、操作环境好、有价元素的综合回收率高、技术成熟等优点,但也存在流程长、操作条件复杂等缺点。
(3)湿法——火法联合工艺处理铜烟尘
采用联合法处理铜烟尘时,铜、锌的回收工艺与全湿法回收铜锌的工艺基本相同,两种方法的主要区别在于浸出渣的处理工艺上,联合法使用火法处理浸出渣。按浸出方式的不同,联合法处理铜烟尘可分为水浸、酸浸、氯盐浸出等方法,其中使用最多的是水浸和酸浸。
(4)水浸—火法工艺
铜烟尘中主金属铜、锌、铅主要以硫酸盐形式存在,铋以氧化物形式存在,由于铜、锌硫酸盐易溶于水,铅、铋化合物难溶于水,因此,采用水浸处理铜烟尘可有效使铜、锌与铅、铋分离。浸出液经处理后回收铜、锌、铟、镉等有价元素,浸出渣则使用反射炉或鼓风炉熔炼回收铅、铋等有价元素。
采用水浸——火法的工艺从含 Cu 12.73%、Pb 13.18%、Zn 8.98%、In 0.046%、Ag238g/t的铜烟尘中回收铜、铅、锌、铟、银。铜烟尘经水浸后,首先对浸出液进行氧化除铁,随后加石灰控制 pH分离与回收铜、锌,得到纯度达96%以上的硫酸铜和纯度达98%以上的硫酸锌。In和Pb、Ag在铜烟尘的水浸过程中被富集到渣中,其后采用酸浸将In与Pb、Ag分离,浸出液用P——做萃取剂,并经反萃、置换后获得纯度达80%以上的海绵铟。银、铅渣采用硫脲浸出法分离银、铅,银的回收率在95%以上,浸出银后的含铅渣用反射炉熔炼回收铅。
以含Cu2.26%、Pb30.30%、Zn 10.79%的铜烟尘为原料回收铜、铅、锌。烟尘在液固比为5的条件下加水进行常温搅拌浸出40min,铜、锌的浸出率可达85%以上,浸出液进行铜、锌分离后生产海绵铜和硫酸锌。浸出渣中铅含量升高到57.5%,经鼓风炉熔炼回收粗铅,铅回收率可达75%以上。该工艺流程短,设备简单,废液可循环使用,二次污染小,铜、铅、锌三种金属的回收率高。水浸——火法处理铜烟尘因浸出过程中不加酸,对设备的腐蚀较小,且浸出液中游离酸较少,更利于对溶液中铜与锌的回收。
(5)酸浸——火法处理铜烟尘
酸浸法处理铜烟尘,流程与水浸法基本相同,但更有利于铜、锌等有价元素的浸出。日本佐贺关冶炼厂采用“硫酸浸出——加铁盐除砷——控制 pH除锌——砷酸铁沉淀硫酸浸出——浸出液加氢氧化钠脱砷——滤液中和回收其他金属”的工艺处理铜烟尘,铅笔造经鼓风炉熔炼回收铅和铋,锌以氢氧化锌形式回收并作为锌冶体厂原料使用,砷形成稳定硫化物进行回收,其余残渣返回铜冶炼厂处理。
酸浸一鼓风炉熔炼的工艺处理铜烟尘回收其中的铜、锌、镉、铟、铅、铋。铜烟尘酸浸液用P—萃取回收铟,铟的回收率可达95%。萃余液加铁置换回收铜得到品位为55%的海绵铜,其后将溶液氧化除铁,加锌粉置换回收溶液中的镉经浓缩结晶回收其中的锌。酸浸渣采用鼓风炉熔炼一铅铋合金电解——高铋阳极泥熔炼的工艺回收铅、铋。湿法一火法联合工艺处理铜烟尘虽然部分解决了砷和铝的污染问题,但仍然存在工艺流程长、操作条件复杂和环境污染大的缺点。
(6)选冶联合法处理铜烟尘
近年来,选冶联合工艺在铜烟尘的综合利用上也得到了应用。铜烟尘经浸出和固液分离后,浸出液经置换法回收铜、沉淀法除砷铁后,溶液进行蒸发、浓缩生产硫酸锌,浸出渣通过浮选或重选产出铅精矿及铜精矿,进一步简化了工艺流程。含有1.45% Cu、35.50% Pb、10.20% Zn、0.86% Cd、2.06% Bi、1.03% As 0.038% In、2.40% Fe和12.90% S的铜烟尘在120~130℃、硫酸浓度74~98g/L、液固比为3~5的条件下加压酸浸2~3h,烟尘中80%的砷进入溶液,铜的浸出率小于液固比10%,实现了铜和砷的有效分离。将浸出液中的砷、铁除去后,采用常规湿法冶金的方法回收锌、镉、铟,分别产出硫酸锌、海绵镉和海绵铟,溶解的砷和铁以砷酸铁的形式沉淀入渣。浸出渣中的铋采用H,SO4-NaCl溶液浸出,铋浸出率为93%,浸出液用铁粉置换得到海绵铋。浸出铋后的浸出渣采用浮选方法回收铜和铅,分别得到铜精矿和铅精矿。
铜烟尘先用水浸,然后通过固液分离、浸出液置换沉铜、调节 pH 除铁、砷,除铁、砷后的浸出液浓缩结晶生产七水硫酸锌,浸出渣采用重选分离出铜精矿、次精矿、中矿和尾矿,铜大部分富集于精矿和次精矿中,铜的回收率达98%,可直接返回铜熔炼工序,渣中砷则富集于尾矿。该工艺铜的总回收率可达98.15%,且实现了杂质开路,大大减轻了后续工艺除杂的压力。选冶联合工艺的分离成本低、污染小,具有良好的应用价值,同时可以实现砷在尾矿中的富集,便于集中处理。
与传统火法回收工艺相比,全湿法工艺、湿法—火法联合工艺和选冶联合工艺由于污染小、金属回收率高、劳动条件好等优点,将在铜烟尘的综合利用过程中具有明显的应用前景。同时,在选择铜烟尘处理工艺时,应从原料成分和性质出发,选择合适的处理工艺,以降低生产成本,使效益最大化。
针对成分如表6-18所示的含锡炼铜烟尘,采用浸出———置换—沉淀的全湿法工艺综合回收其中的铅、锡、铋、铜、锌和银,分别产出铅渣、海绵铜、海绵铋、
锌渣和锡渣,银富集在铋渣中,砷以稳定性比较好的砷酸铁的形式进入渣中。原则工艺流程如图6-6所示。
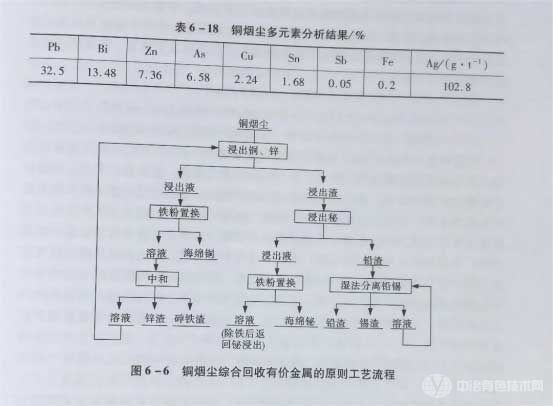
各产物的主要成分为:铅渣 >70% Pb、海绵铋 >45% Bi、Ag >500 g/t、海绵铜 >30% Cu、锡渣 >20% Sn、锌渣 >30% Zn。各有价金属的回收率为铅>90%、铋>96%、铜>90%、锌>90%、银>98%、锡>95%。可见,铜烟尘中的铅、锡、铋、铜、锌、银等有价金属都得到了较好的回收,砷得到了无害化处理。
(7)铅烟尘的处理方法
国内炼铅企业通常将铅烟尘返回与原料混合后继续冶炼,以回收利用烟尘。由于近年炼铅原矿的铅品位下滑,导致烟尘中锌、镉、铜等重金属增多,返回冶炼会降低精矿品位且严重影响炉况。近年来对烟尘的综合利用开展了大量研究,如用硫酸浸出法将烟尘中的铅富集到浸出渣中,而其他大量金属进入溶液中,再用氯化钠溶液浸出铅;用浓硫酸焙烧—水浸法提取烟尘中的大量金属,用氨浸法由烟尘制取ZnO等。