性能和成本是材料技术发展永恒的两大驱动力,而轻量化、整体化、结构功能一体化是飞行器结构设计、材料应用和制造技术共同面临的挑战。在过去的几十年里,诸如热等静压、注塑成形、放电等离子烧结等近净成形技术在钛合金领域获得了长足的进步,但氧含量、孔隙率等瓶颈问题依然没有得到有效解决,因此制约了其在航空钛合金结构制造中的应用。
从科学探索与发展角度看,现代工业需要具有高强度、断裂韧性和刚度,同时尽可能减轻重量的结构材料。因此,钛和铝等轻质高强合金以及Ni基高温合金等承载耐热合金成为了各国新材料研发计划的焦点。此外,这些材料也是激光增材制造中的重要应用材料。
钛合金具有高比强度、比刚度和良好的耐腐蚀性能,满足了飞机高机动性、高可靠性和长寿命的设计需要,其应用水平已成为衡量飞机选材先进程度的一个重要标志。
钛合金和铝合金因其出色的低密度和结构强度而在航空航天、汽车、机械制造等领域被广泛应用。尤其在航空工业中,它们扮演着十分重要的角色,是航空工业的主要结构材料。尽管钛合金比铝合金重约三分之二,但其固有强度意味着可以使用更少的量达到所需要的强度。钛合金因其强度和低密度而成为降低燃料成本的重要材料,被广泛用于飞机喷气发动机和各类航天器。铝合金是现阶段应用最广、最常见的汽车轻量化材料,其密度仅是钢的三分之一。有研究表明,铝合金在整车中最多可以使用540kg,这样的情况下汽车将减重40%。奥迪、丰田等品牌的车辆采用全铝车身就是很好的例子。
由于两种材料都具有高强度和低密度,因此在选择合金时,必须考虑其他因素。
在需要高强度和低重量的关键情况下,每一克都很重要,但如果需要更高强度的部件,钛是最好的选择。因此,钛合金被用于制造医疗器件/植入体、复杂卫星组件、固定装置和支架等。
成本方面,铝是机加工或3D打印最具成本效益的金属;而钛的成本较高,但轻质零件给飞机或航天器节省的燃料将带来巨大效益,同时钛合金零件的使用寿命更长。
在热性能方面,铝合金具有很高的导热率,常被用来制造散热器;对于高温应用,钛的高熔点使其更加适合,航空发动机中就包含大量的钛合金部件。
钛的耐腐蚀性和低反应活性使其成为生物相容性最高的金属,被广泛用于医疗(如手术器械)领域。Ti64还可以很好地抵抗盐分环境,并经常用于海洋应用。
在航空航天领域,铝合金和钛合金都被广泛应用。钛合金具有高强度和低密度(仅为钢的57%左右)的优点,其比强度(强度/密度)远超过其他金属结构材料,可制作出单位强度高、刚性好、质量轻的零部件。飞机中的发动机构件、骨架、蒙皮、紧固件及起落架等都采用了钛合金。另外,3D打印技术参考查阅相关资料发现,铝合金适合在200℃以下的环境中工作,空客A380机身使用的铝材占到了1/3以上,而C919也大量采用了常规高性能铝合金材料。飞机蒙皮、隔框、翼肋等部分都使用了铝合金。
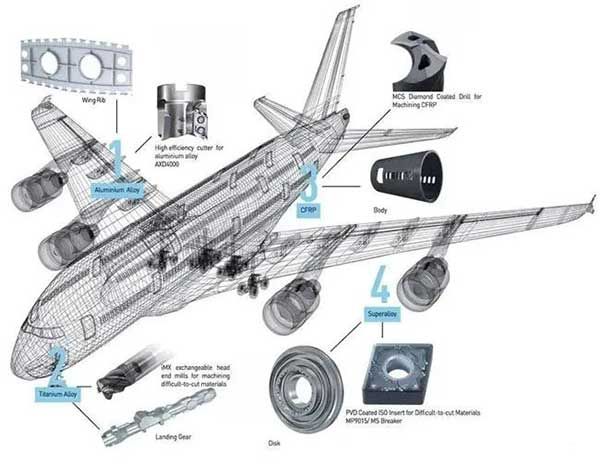
钛合金由于其高熔点和难加工性质,成为了成本最高的金属材料之一。然而,Ti6Al4V钛合金的轻量化、高强度和耐高温特性使其在航空航天领域备受瞩目。它的应用范围包括发动机风扇和压气机低温段工作的叶片、盘、机匣等零件,工作温度区间可达400-500℃。此外,它还用于制造机身和太空舱组件、火箭发动机箱以及直升机旋翼桨毂等。然而,由于钛的导电性较差,它在电气应用中并不是理想的选择。尽管钛合金价格相对较高,但它的耐高温和耐腐蚀性是无法被其他轻质金属所取代的。

铝基合金具有密度低、比强度高、耐腐蚀性强、成形性好等优良物理特性和力学性能,因此在工业中应用广泛。然而,从增材制造成形工艺角度看,铝合金的密度较小,粉体流动性相对较差,在SLM成形粉床上铺放的均匀性较差或在LMD过程中粉末输运的连续性较差,因此对激光增材制造装备中铺粉/送粉系统的精度及准确性要求较高。
目前应用于增材制造的铝合金主要是Al-Si合金,其中具有良好流动性的AlSi10Mg和AlSi12得到了广泛研究。然而,由于Al-Si系合金属于铸造铝合金,尽管采用经过优化的激光增材制造工艺进行制备,但其抗拉强度仍难以突破400MPa,限制了其在航空航天等领域服役性能要求更高的承力构件上的使用。

现代航空航天构件面临着一系列严苛的要求,包括轻量化、高性能、高可靠性和低成本。这种复杂的结构设计和制造难度极大。通过创新和发展航空航天典型铝、钛、镍基构件的激光增材制造技术,我们不仅可以实现选材上的轻量化和高性能化,而且可以体现增材制造技术的精密化和净成形化发展趋势。通过实现材料-结构-性能的一体化增材制造,我们可以将增材制造技术应用于航空航天领域中的重大工程。