转炉黏渣的原因及处理措施有哪些?
答:转炉黏渣的原因与现象:
(1)渣过吹。冰铜造渣吹炼到终点(白冰铜中残留的FeS含量约为1.0%~2.0%时),而未及时放渣,造成大量的磁性氧化铁生成,并且渣层温度降低,导致渣发黏,流动性变差。过吹渣冷却后呈灰白色,喷出时正常渣呈圆而空的颗粒。
(2)石英熔剂加入过多。增加SiO₂的量,会使渣黏度增大。钎棒黏结粗糙,且熔体表面有游离石英呈棉絮状,喷出时,渣成团状。
(3)冷料加入过多。冷料加入过多,会使炉体熔体温度偏低,渣黏性升高,炉前取样板黏结厚。特别是冷料块度大,会造成不能及时地熔化并参与反应,致使排渣困难。
(4)石英熔剂晚加或少加。石英熔剂晚加或少加会使一部分FeS氧化成Fe₂O₃,进而形成大量Fe₃O₄,渣黏度增大,易结壳,严重时有大量磁铁产生使钎样带刺,渣量少。
(5)冰铜带渣或底渣量大,而且冷料量未调整好。
转炉黏渣的处理措施:尽量放出渣来,并根据黏渣原因,追加适量的热冰铜,调整石英熔剂量和冷料量,适当地缩短吹炼时间。
转炉吹炼喷炉的原因及处理措施有哪些?
答:(1)因磁铁渣引起的喷炉事故。原因:由于在造渣时投入的石英熔剂量不足,致使部分FeO无法与SiO₂造渣,而继续氧化成Fe₃O⁴生成磁铁渣。这种磁铁渣密度大黏度高且流动性差,使鼓入炉内的气体不易穿透熔体表面渣层,鼓入的气体在熔体内越积越多,当气压大大超过上层熔体的静压时,就会引起喷炉事故。
处理措施:追加半包或一包热冰铜,并加入足够量的石英熔剂后继续进行吹炼作业,使磁铁还原造渣。反应为:
3Fe³O⁴+FeS+5SiO2= 5(2FeO·SiO₂)+SO₂ (3-10)
(2)转炉渣过吹引起喷炉事故。原因:主要是由于放渣不及时而造成渣过氧化,渣温降低,黏度增大,熔体中的气体不能顺利地排出炉口,最后引起喷炉事故。
处理措施:追加适量的热冰铜后,稍吹炼一段时间,待转炉炉温上来后即停风放渣,把前面造好的渣放出炉体后,再加适量的石英,继续吹炼造渣。
(3)造渣期石英加入过量而引起的喷炉事故。原因:造渣过程中若石英加入过多,会使渣性恶化,渣黏度增大,且易在渣表层形成一层絮状物(游离态的石英),致使气体不易排出,造成喷炉事故。
处理措施:追加热冰铜继续吹炼,改变渣型,造出良性渣。
(4)造铜终点前的喷炉事故。原因:造渣期的渣型不好,未排尽渣就强行进入造铜期。当接近造铜终点时,熔体中的硫含量不断减少而使反应热越来越少,这时若熔体表面渣层厚,随着熔体厚度不断降低而渣的黏度加大,把大量气体阻挡在熔体里面,超过一定的限度时便会喷炉。
处理措施:发现有喷炉迹象时,立即将炉子倾转到0°后用残极加料机投入造量的残极以破坏渣层的凝结性,排放出积压的气体,或用残极投入油缸把一些木柴推入炉膛,使渣层与木柴搅拌在一起,木柴燃烧产生的CO₂和热量可破坏渣层的凝结性,此时送风量宜稍微降低,且调整炉子吹炼角度,另外也可停风,倒出底渣后,再继续吹炼。
(5)冷料直投过多而引起喷炉事故。原因:无论造渣期或造铜期,若冷料一次性投入太多,会引起熔体表面温度偏低,熔体黏度大,送风阻力大,往往夹带着熔体呈团块状喷出炉口。
处理措施:及时修正冷料加入量,适当地降低送风量,加大用氧量,调整炉子的送风角度,以尽快促使熔体温度回升,待正常后可恢复以前的作业状况。
如何判断出铜时间?
答:(1)火焰颜色。造铜期末期,硫和其他金属杂质含量已经达到一个较低的水平,放出的热量也降低,炉温明显下降,火焰颜色由乳白色转为红褐色,表明出铜时间到了。
(2)火花。从炉口喷出物颗粒较大,在外面开花,通常称为火花。当炉口冒出的火花消失时,即可出铜。
(3)炉前取样。从炉口用小铁勺取样,倒在干净的铁板上,观察铜水凝结情况。当凝固的试样呈玫瑰红色,可以出铜。
4)炉后判断。快到出铜时,将从炉后插入风口的铁钎取出,若铁钎上覆盖的铜光滑平整,没有隆起,冷却后呈玫瑰红色并有金属光泽,表明可以出铜。
造铜期吹炼终点自动判断的机理是什么?
答:转炉吹炼终点判断主要通过实时采集并在线分析烟气中二氧化硫、氧以及其他元素含量(铜、铅、锌等金属元素),传送到吹炼终点判断软件系统中,并结合原有DCS系统中的锅炉负压、锅炉温度、转炉送风量等数据进行综合分析,从而实现转炉造铜期吹炼终点自动判断。
粗铜过吹时的特征、原因及其处理措施有哪些?
答:粗铜过吹时的特征:烟气消失,火焰暗红色,摇摆不定,炉后取样的黏结物表面粗糙无光泽,呈灰褐色,组织松散,冷却后易敲打掉。
出现粗铜过吹原因有:(1)对造铜终点判断失误所致;(2)因炉体倾转系统故障造成造铜终点已到,但不能及时停风所致。
处理措施:(1)采用高品位固铍(最好采用固态白冰铜)进行还原反应,根据"过吹"的程度来确定固铍的直投量; (2)采用追加热冰铜的办法。视“过吹”的程度确定冰铜加入量,若加入的热冰铜过多还原过头时,可继续进行送风吹炼,直到造铜终点。
转炉渣的成分及处理方式有哪些?
答:转炉渣含铜量较高,通常为2%~4.5%,转炉渣中铜大都以硫化矿物形态存在,少量以氧化物和金属铜形态存在(见表3-6)。转炉渣中的铜必须加以回收,目前主要有两种回收方式:一种是将转炉渣缓慢冷却、破碎、磨细、浮选,产出渣精矿,然后将其返回到熔炼的配料系统;另一种是根据熔炼方法的不同,将转炉渣以液体或固体状态直接加入熔炼炉内。
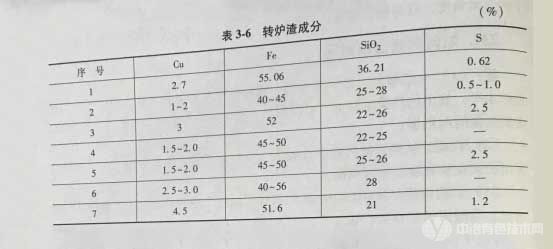
白烟尘特性及处理现状是怎样的?
答:白烟尘是铜冶炼生产过程中产生的固体副产物,收集于转炉工序的电除尘室,其中含有Cu、Zn、Pb、Au、Ag、Bi等有价元素,极具经济价值。同时白烟尘中还含有较高含量的砷,砷主要以As₂O₃、As₂S₃的形式存在,属于可溶性砷,对周边环境存在潜在的威胁。
现阶段,综合利用白烟尘的工艺技术并不完备,部分国内铜冶炼企业多将烟灰直接返回熔炼系统处理降低白烟尘中有价元素含量。白烟尘返回铜熔炼系统后,不仅降低熔炼炉处理能力、恶化炉况,同时炉料中有害成分增多,有害杂质的累积会直接影响产品(电铜)的质量。此外,学术界开展了焙烧、水浸、酸浸、碱浸等方法脱砷除杂,萃取电积回收Cu、Zn,还原精炼Pb、Bi合金的处理方式。
如何提高转炉生产率?
答:转炉的生产率是指每炉每日产粗铜量。在转炉尺寸和冰铜品位一定的情况下,通过增大风压,加大鼓风量,减少管道漏风;缩短停炉作业时间;遵守均衡的温度制度,可以提高转炉生产率。
粗铜的主要成分有哪些?
答:粗铜是冰铜吹炼的主要产物,含铜98.5%~99.0%,另外还有少量的杂质元素如铁、硫、氧、镍、砷、锑、铋、硒、碲及贵金属元素。粗铜主要成分见表3-7。
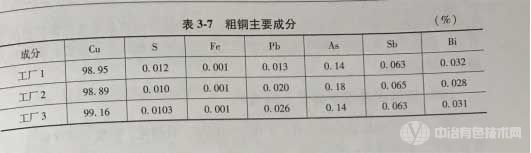
粗铜火法精炼的目的是什么?
答:粗铜火法精炼的目的是除去粗铜中的杂质,并为电解精炼提供优质的铜阳极。在精炼炉中将固体粗铜熔化或直接加入粗铜熔体,鼓入空气,使熔体中与氧亲和力较大的杂质发生氧化,以氧化物的形态形成炉渣或者挥发进入炉气而除去,残留在铜中的氧经还原除去后,浇铸成电解精炼用的阳极板。
铜火法精炼由哪几个过程组成?
答:粗铜火法精炼是周期性作业,反应过程多在反射炉或者回转精炼炉内进行。按照该反应过程的物理化学变化特点和操作程序,每个作业周期基本包括熔化、氧化、还原和浇铸四个阶段。其中氧化和还原为主要阶段。当物料为液态粗铜时,熔化期可以省略。
氧化精炼的原理是什么?
答:氧化精炼的基本原理在于铜中多数杂质对氧的亲和力都大于铜对氧的亲和力,且杂质的氧化物在铜水中溶解度很小。在空气鼓入铜熔体中,杂质便优先氧化除去。铜中有害杂质除去的程度主要取决于氧化过程进行的程度。
氧化精炼中杂质如何分类?
答:按照氧化除去的难易程度,可将杂质分为3类:
(1)铁、钴、锌、锡、铅、硫是易被氧化除去的杂质。它们对氧的亲和力比较大,并且能形成稳定的氧化物进入渣或烟气中而除去。
(2)镍、砷、锑是难以除去的杂质。镍在氧化期缓慢氧化,易与存在的少量砷锑以及铜形成镍云母,导致镍、砷、锑难以除去。
(3)金、银、硒、碲、铋等是不能或很少被除去的杂质。金、银等贵金属氧化精炼时不会氧化;硒碲只有少量被氧化进入炉气中,大部分留在铜中;铋对氧的亲和力和铜相差不大,在精炼时较少除去。
杂质被除去的程度与哪些因素有关?
答:杂质被除去的程度与杂质在铜中的浓度和对氧的亲和力、杂质氧化后所生成的氧化物在铜中的溶解度、杂质及其氧化物的挥发性和杂质氧化物的造渣性有关。杂质及其氧化物在铜中的溶解度越大,该杂质越难除去;杂质对氧亲和力越小,越难除去。
回转式精炼炉有什么特点?
答:回转式精炼炉的特点有:炉体结构简单,自动化、机械化程度较高;炉体容量大,处理量大;密闭性好,炉体热损失小;污染小,有利于环境保护;熔池较深,受热面积小,化料慢,不宜处理冷料。
什么叫稀氧燃烧,有什么优势?
答:稀氧燃烧技术是纯氧助燃燃烧的一种,其主要原理为:以纯氧为助燃介质进行助燃,燃料和氧气通过不同喷嘴高速射入炉膛,高速射流卷吸炉膛内的烟气,燃料和氧气被迅速稀释,在炉膛形成一种漫射的、火焰分布一致的燃烧加热体系。
稀氧燃烧技术的优势有:(1)采用纯氧助燃,热效率高,节约原料,减少排放。相对于传统的助燃风燃烧,纯氧燃烧鼓入风量大大降低,有效减少阳极炉烟气体积,降低了烟气带走的热损失,提高燃烧效率,降低燃耗,同时降低了阳极炉排风机的运行负荷。(2)卷吸炉膛高温烟气的稀释作用,燃烧火焰温度较常规助燃燃烧低,从而降低耐火炉衬的侵蚀,延长炉体寿命,节约生产成本。
如何缩短氧化精炼过程的时间?
答:(1)提高熔剂的造渣率,用压缩风将熔剂直接喷入铜熔体中,增加熔剂与杂质氧化物的接触机会,并且经常变化氧化管插入的位置;
(2)控制铜熔体的温度,一旦出现稀渣,向熔体表面加入石英熔剂,并且及时进行扒渣处理。
氧、氢含量对还原精炼各有什么影响?
答:还原精炼中,氧含量过多会使得铜变脆,延展性和导电性能变差。但是在还原过程中熔体中需要保留一部分氧,用来防止H₂和SO₂溶于铜熔体中,便铜性能变差。
在还原过程中,氢是主要的还原剂之一,可以脱除熔体中溶解的氧,获得组织致密、延展性能良好的铜。若含氢过多,铸成的阳极有气孔,对电解不利。
如何降低铜中的含氢量?
答:为了降低铜中的含氢量,可以采取防止过还原和严格控制铸锭温度的方法。过还原时,由于铜水含氧量极少,氢含量剧增,所以要严格控制氧含量,宁可让熔体中残留微量的氧;由于氢在铜水中的溶解度随温度升高而加大,因此,铸锭温度应尽可能低,减少氢的溶解度。
还原精炼终点如何判断?
答:还原的目的是把氧化后残留在铜水中的Cu₂O还原成金属铜。还原终点的标志是试样断面呈玫瑰红色,结晶致密并具有金属光泽,试样薄片柔软,弯曲不易折断。还原完毕后,扒去浮渣,用木炭或含硫低的石油焦炭覆盖,然后进行浇铸。
什么叫带硫还原,其优势有哪些?
答:无氧化带硫还原就是指粗铜在不经过专门的氧化脱硫操作,直接采用边搅拌边还原的方式一步将粗铜精炼为阳极铜的过程,从而缩短反应时间,减少还原剂的使用。
带硫还原的优势:(1)缩短阳极炉作业时间,提高生产效率,扩大产能; (2)降低还原气体(LPG)的使用量,降低生产成本;(3)由于取消了氧化阶段,降低了重油的使用量。
如何降低精炼渣的含铜量?
答:(1)减少精炼渣数量。处理高品位粗铜时,不必加入熔剂造渣,尽可能地减少渣量。
2)将精炼渣扒干净。在炉渣处于黏稠状态时进行扒渣,最好采用铁柄木耙,在熔池表面扒,尽量避免金属铜被扒出。
(3)减少精炼渣中Cu₂O的含量。向渣层中加入少量还原剂,使渣中过多的Cu₂O还原,但渣中杂质仍保留在渣中。
4)加入熔剂。向熔池中加入廉价的炼钢平炉炉渣,利用FeO置换Cu₂O,达到贫化炉渣的目的。
阳极板浇铸有哪两种方式,各有什么特点?
答:一般浇铸用圆盘型或者直线型浇铸机进行浇铸。圆盘浇铸机结构简单,制造方便,维修容易,机械损坏率小,应用广泛。直线浇铸机占地面积小,结构紧凑,但是维修麻烦,易出现运行不稳的现象,严重影响阳极质量。
浇铸阳极板对熔体温度有什么要求?
答:浇铸温度是获得优质阳极板的重要因素。若铜熔体温度过高,容易增加气体在熔体中的溶解度,在冷凝时易产生气孔;阳极表面不致密,影响浇铸速度;也会使铸模涂料变质,产生粘板现象。若熔体温度较低,流动性不好,影响浇铸质量。熔体温度一般控制在1100℃左右。
铸模的种类及其优缺点是什么?
答:目前,阳极板浇铸的模具主要有铜模和钢模两种,其优缺点比较见表3-8。
浇铸阳极板对铸模温度有什么要求?
答:铸模温度过高,容易导致涂料变质,引起粘板;铸模温度过低,涂料不易干燥,阳极板易产生气孔,所以铸模温度一般控制在120~140℃。