先进燃烧及燃煤工业锅炉工程技术
我国燃煤工业锅炉占全国工业锅炉总量和总蒸发量的85%左右,每年消耗原煤约6.4亿t,占全国煤炭消费总量的23.4%;烟尘排放量为375.2万t,占全国烟尘排放量的41.6%;排放SO519万t,占全国SO排放量的22%;排放氮氧化物250万t左右,仅次于火电行业和机动车,位居全国第三。也就是说,全国的工业锅炉燃烧了20%的煤炭,但排放了40%以上的烟尘。我国工业锅炉的效率低下,虽然设计效率一般为72%~80%,但实际运行热效率大多在60%~65%,比国外先进水平低15%~20%。因为低效,每年多消耗的煤炭约为两亿吨。
先进燃烧及燃煤工业锅炉工程技术包括链条锅炉自动分层燃烧及多煤种节能改造技术;复合燃烧技术(层燃和悬浮燃烧组合,强化炉内燃烧过程,增大蒸发量,提高锅炉燃烧效率与煤种适应性);循环流化床技术(燃料随床料在炉内多次循环,燃料适应性强,燃烧效率高);富氧助燃技术(通过物理或化学方法,得到富氧空气,提升燃烧效率,减少烟气量);蓄热式高温空气燃烧技术(蓄势回收,预热助燃空气,燃料分级燃烧和高速气流卷吸炉内燃烧产物);煤气化分相燃烧技术(以空气和水蒸气为气化剂,实现煤炭气化和气固分相燃烧)。
煤粉燃烧是先进的燃煤技术,包括煤粉接收、储备、输送、燃烧及点火、锅炉换热、烟气净化、自动控制等技术构成的完整、成套、新型工业锅炉技术系统。具有燃烧速度快、燃尽率高、烟气热损失低等优点,可广泛应用于大型锅炉。新型高效煤粉工业锅炉采用煤粉集中制备、精密供粉、空气分级燃烧、炉内脱硫和全过程自动控制等先进技术,实现了燃煤锅炉的高效运行和洁净排放。其关键技术包括全密闭精确供粉、狭小空间煤粉低氮稳燃、锅炉积灰和灰黏污自清洁、除尘脱硫等,是以锅炉为核心的完整技术系统。锅炉系统的运行由点火程序控制器和上位计算机系统共同完成。煤粉燃尽率大于98%,系统运行热效率大于88%,烟尘排放≤30mg/m³,SO排放≤100mg/m³,氮氧化物排放≤200mg/m³。与传统燃煤锅炉相比,新型节能环保型煤粉工业锅炉的节能率达到30%以上,排放的烟尘、SO、氮氧化物等污染物浓度均低于国家标准,而且操作简单,锅炉运行、输煤、燃烧、脱硫除尘、出渣等实现了全自动化控制,煤和渣不落地、不需要堆放场地。与天然气锅炉相比,煤粉锅炉不受管网建设限制,可因地制宜地发展,投资少、见效快,污染物排放指标优于燃油锅炉,和天然气锅炉相近。工业锅炉燃煤污染控制是当前发展洁净煤技术的重点,大力推广使用新型煤粉工业锅炉,对节约能源和治理大气污染都有非常现实的意义。
余热余压余能利用工程技术
余热回收利用原则:生产蒸汽的余热回收设备有余热锅炉和汽化冷却装置等。余热锅炉属低温炉,在高温炉后直接安装效果并不理想,在选用回收利用设备过程中应充分考虑企业余热的种类、介质温度、数量及利用可行性。总原则就是要将回收的余热优先用于自身系统能耗设备,减少一次能源消耗量,且高温余热必须尽可能地用于有高温需求的工艺设备,减少能量转换次数,同时要有相应的安保措施,在发生事故时不影响本体的正常生产。
余热回收利用设备:有色冶金企业废气余热回收利用设备有辐射式换热器管式换热器、片状管换热器、热管换热器、余热锅炉、余热锅炉-汽轮机发电装置等。辐射式换热器是使用较广的换热器,多用在均热炉或加热炉上,助燃效果较好,温度效率超过40%,不过其热回收率仅为30%左右。管式换热器约被40%的钢铁企业所采用,其热回收率平均在26%~30%。片状管换热器在联合企业及中小企业中采用得较多,其热回收率平均为28%~35%。热管换热器在中小企业应用较为广泛,主要用于预热空气或煤气,回收热风炉的烟气余热,热回收率超过50%。余热锅炉在联合企业应用比较多,主要用于平炉,回收的热量中70%用于企业生产。通过电力回收余热是目前最好的利用方式,但余热锅炉-汽轮机发电装置受限于动力设备运转连续性及电力并网等因素。
(2)余热余压余能利用工程技术
有色冶金工业烟气具有如下的特点:热负荷分散、不稳定,工艺波动、间隙式生产;含尘量大,基夫赛特炉竖直烟道入口烟气含尘450~570g/m³(标),含低熔点烟尘时,产生黏结、积灰现象;具有腐蚀性,含有SO、SO、HF、Cl等腐蚀性气体;温度高,大部分冶炼炉烟气超过1000℃,典型有色冶金炉烟气出口温度如表4-5所示。因此,烟气的余热回收利用在技术上有很大难度。
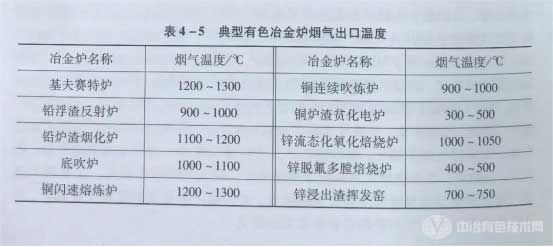
烟气余热资源化的基本原则是梯级利用、系统优化。根据烟气的品质,分温度段回收,减少传热温差(不可逆损失);功率、流量等匹配得当;烟气、被加热对象应避免大温差传热。并且利用对象尽可能在系统内部,系统布置方面使传输距离尽可能短。
推广生产过程余热、余压、余能的回收利用技术,遵循“梯级利用,高质高用”原则,优先把高品位余热余能用于做功或发电,低温余热用于空调、采暖或生活用热。
工业窑炉烟气余热可用于空气、燃料及物料的预热及炉外热回收设施。发展工业窑炉余热、余能利用技术,包括烟气废热锅炉及发电装置;窑炉烟气辐射预热器和废气热交换器;回收其他装置余热用于锅炉及发电;冶炼烟气余热梯级利用回收技术;中低温烟气余热的有机郎肯循环(ORC)发电技术;热电转换低温温差余热发电技术。
高浓度冶炼烟气制酸及硫酸生产余热回收技术
火法炼铜中烟气制酸能耗占总能耗比例较大。传统的制酸工艺,进入转化的烟气SO浓度在10%左右,未对制酸过程中、低温位余热进行回收,吨酸工艺能耗高达90~120kW·h,即330~400kW·h/t阳极铜,折算为106~129kgce/t 阳极铜,约占从铜精矿到阳极铜总能耗的1/3。因此烟气制酸是火法炼铜节能潜力最大的工序。
烟气制酸无论转化还是吸收过程,均是放热过程,不仅不需补充热量,还能对其产生的中、低温位余热进行回收。因此,能耗主要为风机、泵等动力设备耗能。要降低制酸能耗,主要措施为:①实现高浓度SO烟气制酸;②优化系统管路、催化剂等配置,减少系统阻力;③提高机电设备运行效率;④回收制酸中、低温位余热。上述措施的综合利用,已使制酸能耗大幅度降低。目前,国内技术领先的炼铜厂,制酸SO浓度已高达18%以上,且对制酸中产出的中、低温位余热进行了回收,吨酸电耗降低至60kWh,同时可回收低压蒸汽0.38t,扣除回收的余热,制酸不仅不消耗能源,而且还有盈余。仅此一项技术,即可使火法炼铜工艺能耗降低100kgce/t阳极铜以上。