我国铜冶金技术通过引进集成再创新,目前一批企业从规模、技术、装备、能耗、环保、综合回收等多方面,已居于世界先进水平,部分技术和装备已出口国外。铜闪速熔炼技术,铜、铅富氧溶池熔炼新技术,自主研发的“氧气底吹炼铜新工艺”,这些具有世界先进水平的新技术、新工艺在生产中的应用,大大提升了我国重金属冶炼技术水平。铜冶炼先进技术、富氧熔炼、余热回收及大型回转式阳极炉、稀氧燃烧、透气砖通氮气搅拌、自氧化还原等技术和装备的使用,使冶炼过程能耗大幅度降低。烟气浓度升高,烟气量减少,烟气输送动力消耗降低使得制酸能耗进一步降低。另外,奥托昆普闪速熔炼技术朝着高铜锍品位、高氧浓度、高投料量、高热负荷“四高”熔炼方向发展,可进一步实现铜闪速熔炼的高效、节能、低污染。
“双闪”冶炼(闪速熔炼、闪速吹炼)是国际上先进的铜冶炼技术,解决了铜冶炼过程中的低空污染问题,能耗大幅降低。山东阳谷祥光铜业已引进芬兰奥托昆普闪速熔炼和闪速吹炼双闪速炉炼铜技术,被国家环保部评为十大“国家环境友好工程”之一。中条山有色金属集团公司和中国恩菲工程技术有限公司开发的铜锍顶吹吹炼新工艺,有效解决了P-S转炉逸散SO2烟气的低空污染和作业安全问题,粗铜冶炼能耗低于490kgce/t。
我国铜冶炼近年来所取得的成绩,主要得益于企业采用了先进的富氧闪速及富氧熔池熔炼工艺,这种工艺替代了反射炉、鼓风炉和电炉等传统工艺,提高了熔炼的强度,降低了能耗,减少了二氧化硫的排放。闪速炉、转炉、反射炉及自热炉尾部均设置余热锅炉,充分回收利用余热资源生产蒸汽,每年生产余热饱和蒸汽70多万t。在“十二五”期间,氧气底吹炉连续炼铜技术、闪速炉短流程一步炼铜技术、新型侧吹熔池熔炼等铜冶炼工艺的短流程研发成功和推广,是铜冶炼节能减排的重要途径。
硫化铜精矿火法炼铜包含造锍熔炼、吹炼、火法精炼和电解精炼等主要工序。其中,造锍熔炼是最核心的环节。铜冶炼节能减排主要归因于造锍熔炼技术的进步。造锍熔炼工艺的技术进步,主要体现在新一代的强化熔炼技术——闪速熔炼和熔池熔炼,取代了传统的鼓风炉、反射炉和电炉熔炼,实现了节能及SO2 减排。
表4-3所示为火法炼铜造锍熔炼新技术工业应用年份。

20世纪70年代得到工业应用的熔池熔炼技术有白银法、诺兰达法、三菱法、特尼恩特法和瓦纽科夫法。①白银法是我国自主研发的第一种炼铜方法,20世纪70年代由中国白银有色金属公司及国内其他单位联合开发,1979年正式命名为“白银炼铜法”,是一种反射炉改良技术,属侧吹熔池熔炼。白银炉历经多次改进:其一是由单室炉改为双室炉(103m²,熔炼区与炉渣贫化区分开);其二,由空气熔炼改为富氧熔炼。目前,白银炉富氧浓度为45%~55%;第三,近年来,白银公司与中国瑞林工程技术有限公司合作,对炉体结构等进行了改进,延长了炉龄,提高了产能【目前达10万t Cu/(炉.a)】,改善了车间环境。目前,白银公司有2台100m²白银炉在运转,粗铜产能20万t/a。②诺兰达法是中国引进的第二种炼铜工艺,湖北大冶有色金属公司在20世纪90年代初引进应用。目前,大冶公司诺兰达炉已为澳斯麦特炉取代。③三菱法属非浸没式顶吹熔池熔炼,是世界上第一种成功工业应用的连续炼铜工艺,由日本三菱公司研发成功。中国没有引进三菱法。④特尼恩特炉可单独处理铜精矿生产高品位铜锍。特尼恩特法在智利得到广泛应用,目前,智利有5座炉子运转,年产铜约70万t。特尼恩特法在中国没有得到应用。⑤瓦纽科夫法属侧吹熔池熔炼技术。2000年以来,我国逐步掌握该技术,用于炼铅、炼铜等方面,由此该法在我国又称为“金峰炉”“侧吹炉”“双侧吹炉”等(统一称其为双侧吹炉)。目前,
我国至少有3座双侧吹炉正常运行,用于造锍熔炼(金峰、富邦、和鼎),粗铜产能约30万t/a。
在我国铜冶炼中,除奥图泰型闪速熔炼外,另一项得到广泛应用的技术是浸没式顶吹(TSL)熔池熔炼法(艾萨法和澳斯麦特法)。目前,TSL技术广泛应用于铜、镍、铅、锡、锌、电子废料及工业垃圾处理等领域。在全球有数十座炉子在运转。我国铜冶金方面有9座炉子用于造锍熔炼和吹炼,其中澳斯麦特炉7座,艾萨炉2座。除白银法外,底吹炉熔炼是中国拥有自主知识产权的另一项炼铜技术。1990—1993年,中国恩菲公司及水口山有色金属公司等单位,在氧气底吹炼铅试验装置上,开展了3000 t/a铜富氧底吹造锍熔炼半工业化试验,取得初步成功。故该法又称为水口山(SKS)炼铜法。1994——1995年,中国恩菲公司、中科院过程所和中条山有色金属公司,联合开展了底吹炉炼铜放大冷态模型研究。2001 年,中国恩菲公司采用富氧底吹法为越南建成1万t/a的大龙铜冶炼厂,标志着该技术得到工业应用。2005年,山东方圆公司采用富氧底吹技术,建设规模为5~10万t/a炼铜厂。2008年建成投产,标志着富氧底吹成为较为成熟的炼铜技术。随后,国内又采用该技术相继建成山东恒邦、内蒙古包头华鼎、山西垣曲等炼铜厂。
在火法炼铜节能减排进程中,新的强化熔炼技术及氧气的应用,起到了决定性的作用。氧气的应用及富氧浓度的提高,使得烟气量减少,烟气SO2,浓度提高,对铜冶炼节能减排起到了关键作用,各种炼铜方法富氧浓度如表4-4所示。工艺模拟表明,在造锍熔炼中,使用1t0可节能5440MJ,制氧厂生产1t0,耗电285kW.h,电厂发电效率按38%计算,抵消制氧能耗后,净节能为2740MJ,折合93.6 kgce。
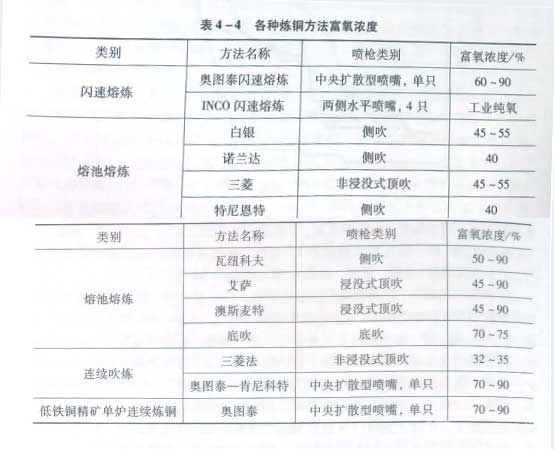
图4-8所示为1960—2007年世界铜冶炼工业SO2捕集情况。由图可见,在20世纪60——70年代,世界主要铜冶炼国家和地区中,仅日本和西欧SO2捕集率达到较高水平,而当时美国、智利和中国铜冶炼烟气中SO2都几乎没有回收。而到2007年,全球铜冶炼SO2捕集率均达到90%左右。以方法而论,双闪法和三菱法,由于实现了连续吹炼,生产中基本消除了SO2的无组织排放,SO2捕集率均超过99.5%,是SO2,排放量最低的火法炼铜工艺。在造锍熔炼—P-S转炉吹炼炼铜工艺中,奥图泰型闪速熔炼由于炉体密封较好,SO2捕集率较高,可以达到99%以上。其他熔池熔炼法,SO2捕集率在98%~99%,但炉体固定的熔池熔炼炉,SO2无组织排放比炉体转动的稍少。
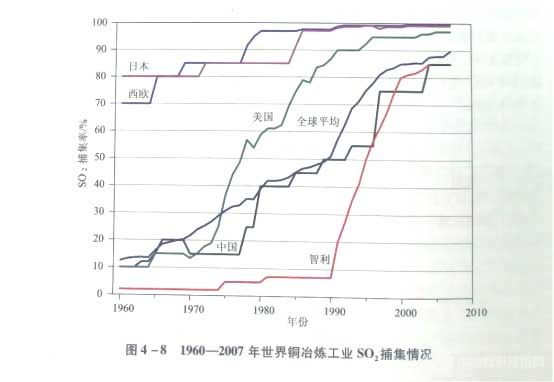