肯尼科特-奥图泰连续吹炼
1)方法简介
美国肯尼科特铜公司Garfield炼铜厂原采用P-S转炉工艺生产,为满足美国犹他州日趋严格的环保标准,以及降低生产成本,20世纪70年代末提出了“固体铜锍氧化连续吹炼”专利,开展了实验。20世纪80年代中期,与在闪速炉熔炼技术上具有优势的奥图泰公司合作,共同进行闪速吹炼技术研发及推广,在奥图泰公司Pori研发中心进行的半工业试验取得了很好的结果,在此基础上,1995年Garfield炼铜厂建成闪速吹炼系统,取代P-S转炉吹炼。因此,目前这一技术为肯尼科特公司与奥图泰公司共有,称之为肯尼科特-奥图泰闪速吹炼。
闪速吹炼炉与闪速熔炼炉结构大致相同,只是炉体规格要小得多,但由于粗铜比重大、浮力强,以及铁酸钙炉渣腐蚀性强等原因,在炉体结构细节上,如冷却水套、炉衬,特别是炉底结构等方面,进行了许多改进。Garfield炼铜厂闪速吹炼炉前期炉寿命较短,其间发生过2次跑铜事故,通过不断改进,从第6炉期开始,炉寿命提高至5年以上,祥光铜业第1炉期炉寿命即达3.5年。预期今后炉寿命完全可能达到7~10年。
图3-33为闪速吹炼炉示意图。我国已投产的2座闪速吹炼炉,产能均按40万tCu/a设计,其规格略有不同。祥光铜业闪速吹炼炉内部尺寸为:反应塔直径4.3m,高6m,池中心距11.6m。铜陵金冠铜业闪速吹炼炉内部尺寸为:反应塔直径5m,高7m,沉淀池长21.8m,宽6.7m,高2.1m。
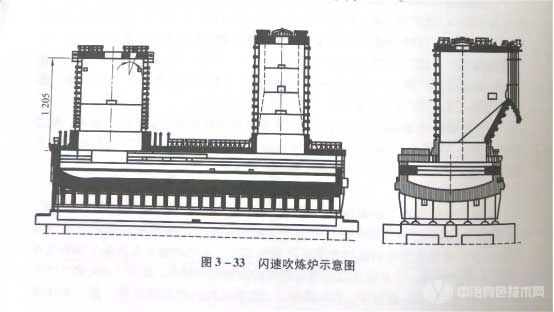
图3-33 闪速吹炼炉示意图
图3-34所示为双闪法炼铜工艺原则流程图。肯尼科特-奥图泰闪速吹炼(以下简称闪速吹炼)除可以与奥图泰闪速熔炼配套外,也可与其他能产出70%左右高品位铜锍的任何熔炼方法结合,由于其处理能力强,今后甚至可以将异地多个厂家产出的高品位铜锍,汇集在一座闪速吹炼炉处理,这点是闪速吹炼相较于三菱法吹炼较大的优势所在。
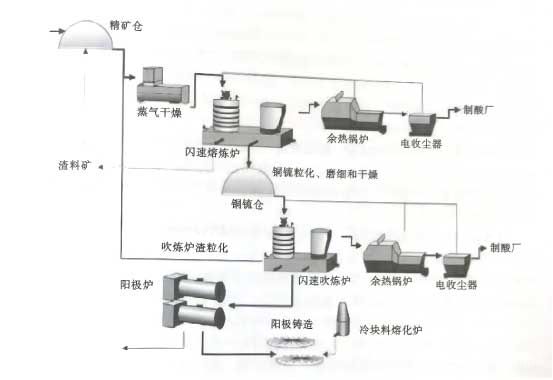
图3-34 闪速熔炼一肯尼科特-奥图泰闪速吹炼工艺
熔炼炉产出的铜锍,品位控制在67%~72%,SiO含量控制在小于0.5%,水淬后磨细干燥至粒度为48μm左右,水分小于0.3%,气动输运到炉顶料仓。然后,通过喷嘴将其与熔剂石灰和少量石英砂、吹炼烟尘及80%左右的富氧空气一并喷洒进入反应塔中,在1400℃左右高温下,发生铜锍吹炼的物理化学反应,生成粗铜(Cu 99%,S 0.3%)、铁酸钙炉渣(Cu 20%,Ca0/Fe 0.37,Fe,0.30%,SiO2.5%)及SO烟气(SO40%,烟尘率5%,烟尘95%为硫酸盐),这一反应过程可能持续到熔池中才结束。粗铜和炉渣熔体在沉淀池中沉淀分离,分别定期从排铜口和排渣口排出。粗铜通过流槽排放至回转式阳极炉中火法精炼。炉渣通过流槽排出后水淬,水淬渣干燥磨细后输送至熔炼系统处理。烟气与烟尘经直升烟道进入余热锅炉回收余热,再经电收尘、湿式洗涤、电除雾后进入制酸系统。
与三菱法相同,闪速吹炼也采用CaO溶剂,造铁酸钙炉渣。这一炉渣体系有下列优点:①对FeO溶解能力强,熔点低,在粗铜含S0.3%,渣含Cu20%的情况下,炉渣可正常放出;②CuO在其中的活度系数小,渣含铜较铁橄榄石炉渣低;③对砷、锑等杂质脱除能力强,但脱铅铋能力较低。铁酸钙炉渣体系对SiO,溶解度极小,当其中SiO含量超过5%,即可能过饱和析出,因此,对铜锍中夹带的SiO,应严格控制,不能超过0.5%,在P-S转炉吹炼中,则不存在这一问题。但由于铁酸钙炉渣对炉衬腐蚀性强、流动性好,因此,为了不致过分冲刷炉衬,以及达到对炉衬挂渣保护的要求,对其中Fe,O的量和过饱和度也应控制恰当。正常吹炼中,除通过调节料/O,比控制粗铜含S外,还要控制渣中Ca/Fe比在0.3 ~0.45(一般为0.37),SiO,含量在2.5%,这样,渣中Fe,O么大致在30%,就既能保证炉渣有足够的流动性,能够从炉内正常放出,而流动性又不至于太高,过分冲刷炉衬,同时还能对炉衬挂渣保护。
闪速吹炼生产中,应对渣型、粗铜质量、渣温实现稳定控制。铜锍、炉渣、粗铜成分定期取样快速测定,渣温测定以沉淀池顶温度为准,每小时测定1次。将这些测定数据输入计算机,根据控制模型计算结果对相关工艺参数进行自动调控,以使过程稳定进行。
渣含铜控制目标值为20%。生产实践表明,渣含铜与粗铜含S大致成反比,在渣含Cu20%时,粗铜含S为0.3%,含0为0.35%。渣含铜主要通过调节氧系数(0/铜锍)控制。每2h取1次干燥铜锍样化验为反馈控制提供依据,每1h 由沉淀池顶取棒渣样,为反馈控制提供依据。炉渣m(CaO)/m(Fe)比控制在0.3~0.45,正常目标值为0.37,通过调节溶剂Ca0加入量控制。操作经验表明,CaO/Fe比大于0.45,CaSO&会在沉淀池表面结壳;小于0.3,Fe,O.会过饱和析出沉淀,随粗铜排出,黏结在粗铜流槽和阳极炉内。渣中Fe。O么含量与炉渣含铜、CaO/Fe比、SiO含量等相关,控制渣含铜20%,m(Ca0)/m(Fe)比0.37,SiO,含量2.5%时,渣中FeO含量为30%。渣中SiO含量控制在约2.5%,通过调节溶剂SiO,的加入量控制。炉渣中少量SiO存在,可调节炉渣流动性及FeO的饱和程度,提高炉衬寿命。粗铜质量主要是控制其中的S含量,目标值为0.3%,通过调节氧系数控制。从原理上讲,氧系数是根据物料平衡计算确定的,因此,与铜锍品位、烟尘返回与否及其成分等有关。粗铜中As、Sb、Bi、Pb等杂质含量,主要与原料成分、烟尘返回走向等有关。Garfield炼铜厂实践表明,在铜精矿杂质含量偏高,烟尘直接返回的情况下,粗铜中杂质含量有增高的趋势,说明杂质元素在系统中有循环累积,此时,应对部分高含杂烟尘采用湿法处理,使部分有害杂质开路。目标渣温为1270±20℃,目标铜锍温度为1250℃,允许在1240~1270℃范围内波动,通过调节烟尘加入量和富氧浓度控制。
2)技术特点
①以CaO为熔剂,造铁酸钙炉渣,降低形成泡沫渣的风险,较之铁橄榄石渣型,该炉渣含铜低,对砷、锑等杂质脱除能力强,但脱铅率低。
②闪速吹炼中,炉膛内只有粗铜和炉渣两个熔体相,粗铜含S0.3%左右。③环保。消除了P-S转炉炉口SO泄露及铜锍、粗铜包子吊运中SO的逸散,烟气量及SO浓度的稳定有利于制酸,硫捕集率高,生产现场环境好。Garfield炼铜厂1999年硫捕集率达到99.9%,每生产1t铜SO排放量小于2kg,该厂1998年PM10总排放量234 t,仅为政府限定允许排放量的56%。
④闪速吹炼处理冷态固体铜锍,可与任何能产出70%左右高品位铜锍的熔炼工艺配套使用,而且可将多座熔炼炉产出的铜锍集中在1座吹炼炉中处理。
⑤投资及运行费用低。对年产30~40万t的炼铜厂,采用闪速吹炼,在投资和运行成本方面,可降低20%左右。这主要归因于以下几点:第一是1台吹炼炉可取代4~5台P-S转炉;第二是闪速吹炼烟气量小,SO浓度高,流量及浓度稳定,使得余热回收、除尘及制酸系统投资及运行成本大幅度降低。第三是炉体寿命长,耐火材料消耗低。
⑥双闪法是目前能耗最低的炼铜方法之一。与三菱法比较,能耗更低。⑦闪速吹炼铜锍需要水淬磨细干燥,不仅不能利用其热量,还要额外耗能。⑧闪速吹炼不能处理块状冷料,如残阳极、流槽结壳等。
3)技术指标
①富氧浓度:常温,80%0;
②铜锍品位:69%~71%;
③炉渣CaO/Fe比:0.33~0.39;
④炉渣SiO含量:1.5%~2.5%;
⑤粗铜成分:Cu98.5%~99.3%,S0.3%,00.25%;
⑥炉渣成分:Cu20%,Fe030%;
⑦烟气SO浓度:30%~40%;
⑧烟尘率:8%~9%;
⑨粗铜温度:1230~1270℃;
⑩炉渣温度:1250~1290℃。
4)国内外应用情况
到目前为止,世界上已有4座闪速吹炼炉建成投产,这些闪速吹炼炉均与闪速熔炼配套使用,即所谓双闪法炼铜。世界首座闪速吹炼炉1995年在美国肯尼科特公司Garfield炼铜厂建成,规模为年产铜30万t,一次投产成功并很快达产,初期存在炉体寿命短等问题,经改进炉体寿命已提高至5年以上。该厂闪速吹炼工艺已运行18年,标志着闪速吹炼技术已较为成熟。其余几座闪速吹炼炉都在我国。2007年,山东祥光铜业公司双闪法系统建成投产,规模为年产铜40万t,一期20万t,该厂整合了多项先进工艺和装备,是世界上最先进的炼铜企业之一。
2011年,达到年产40万t铜规模。2012年,铜陵有色金属公司金冠铜业公司建成一套双闪法系统投人生产,规模为年产铜40万t。金川有色金属公司在广西防城港建设一套年产40万t铜的双闪法系统,2013年建成投产。
5)总体评价
闪速吹炼的发明及推广应用,是炼铜技术发展的一个重大成就。自20世纪后半叶开始,一系列先进的火法炼铜熔炼技术逐步取代了鼓风炉、反射炉和电炉,使得过程得以强化,实现了高效、节能、低污染。相比较而言,吹炼技术的进步相对滞后。传统的P-S转炉吹炼,由于效率低、设备台数多、间断操作、SO,泄漏及逸散问题难以彻底解决,已成为火法炼铜技术进一步向高效节能、环保清洁方向发展的制约环节,长期以来,冶金工作者一直致力于连续炼铜、连续吹炼技术的研发,但截至目前,仅有三菱法和闪速吹炼得到推广应用。而三菱法吹炼由于与其他熔炼方法配套存在一些问题,加之其能耗偏高,难以广泛推广应用。因此,可以预期,P-S转炉吹炼将逐步为闪速吹炼所取代,但由于铜冶炼项目投资巨大等原因,这一过程将很漫长。