铜渣处理与资源化技术
(1)铜渣的火法贫化
返回重熔和还原造锍是铜渣火法贫化的主要方式。炉渣返回重熔可回收铜得到的铜锍返主流程,炉渣的钴、镍回收采取在主流程之外的单独还原造镜。渣贫化方法很多,熔炼工艺是确定炉渣贫化工艺技术的主要因素,含铜炉渣的火法贫化基于以下反应:
3FeO+FeS——10Fe0+SO (6-6)
(Fe,Co,Ni)0FeO+C—→CoO+NiO+3FeO+CO (6-7)
2(Co,Ni)0SiO+2FeS——2FeOSiO+2(Co,Ni)S (6-8)
为降低渣中FeO含量,还原可使FeO转化为FeO并与加入的石英熔剂造渣以改善铜锍的沉降分离,并产生了一些新的贫化方式。①反射炉贫化:反射炉是炉渣贫化传统方法,在炉顶采用氧/燃烧喷嘴的反射筒形反应器,将含铜和磁性氧化铁矿物分批装人,通过风口喷粉煤、油或天然气进入熔池,还原磁性氧化铁使含量降低到10%,然后分离出熔融渣中铜锍,这种方法至今仍在日本小名浜冶炼厂和智利的卡列托勒斯炼铜厂应用。②电炉法贫化:用电炉提高熔体温度使渣中铜的含量降低,同时还原熔融渣中氧化铜,回收熔渣中细颗粒铜。电炉贫化不仅可处理各种成分的炉渣,而且还可以处理各种返料,电能在电极间的流动产生搅拌作用,可促使渣中的铜粒凝聚长大。③真空贫化:炉渣真空贫化使诺兰达富氧熔池炉渣1/2~2/3的渣层含铜量从5%降到0.5%以下,真空贫化可迅速消除或减少Fe。O而降低渣的熔点、黏度和密度,以提高渣-锍间的界面张力而促进渣-锍分离。真空的作用是迅速脱除渣中的SO气泡,利用气泡的迅速长大上浮对熔渣进行强烈搅拌,增大了锍滴碰撞合并,但存在的主要问题是成本较高和操作复杂。④渣桶法:用渣桶作为沉淀池为常用的降低废渣含铜的一种最简便的方法,其关键是保持桶内炉渣温度,回收桶底富集的部分渣或渣皮再处理,利用渣的潜热来实现铜滴沉降和晶体粗化。⑤熔盐提取:利用铜在渣中与铜锍中的分配系数差异,以液态铜锍为提取相使其与含铜炉渣充分接触,从而提取溶解和夹杂在渣中的铜,该方法用于处理哈萨克斯坦的瓦纽科夫法产生的炉渣取得较好的效果,此外最近熔盐提取出现了直流电极还原和电泳富集等方法。
(2)炉渣选矿
利用金属赋存相表面亲水、亲油性质及磁学性质的差别,通过磁选和浮选分离富集。铜渣黏度大,阻碍铜相晶粒的迁移聚集使晶粒细小,造成铜相中硫化铜的含量下降,使铜选矿困难。①浮选法:从富氧闪速熔炼渣和转炉渣中浮选回收铜在工业上已广泛应用,浮选法铜收率高且能耗低,将FeSO▲等杂质除去可降低吹炼过程石英消耗,回收率达90%以上,尾渣含铜0.3%~0.5%。②磁选法:铜渣中强磁相为铁合金和磁铁矿,钴、镍在铁磁矿物中集中,铜存在于非磁相,世界上多家铜冶炼厂用选矿方法回收转炉渣中的铜。
(3)湿法浸出
湿法过程可克服火法贫化过程的高能耗以及产生废气污染的缺点,其分离的良好选择性更适合于处理低品位铜渣。①直接浸出:炼铜炉渣中Cu、Ni、Co、Zn 等金属的矿物可经氧气氧化而溶于稀硫酸介质中。随着铁的溶解,损失在渣中的铜及占据部分Fe晶格的钴、镍等被释放出来,实践中采用0.7mol/L硫酸在氧压0.59 MPa及130℃条件下单段浸出转炉渣,铜浸出率达92%,镍钴浸出率大于95%。②间接浸出:预处理可改性铜渣中的有价金属赋存状态,使其易于分离回收,氯化焙烧和硫酸化焙烧为常用的方法,焙烧产物直接水浸,酸性FeCl浸出经还原焙烧的闪速炉渣及转炉渣的镍钴浸出率分别达95%和80%。③细菌浸出:细菌浸出能浸溶硫化铜,因其具有一系列优点而快速发展。但细菌浸出的最大缺点是反应速度慢、浸出周期长,通过加入某些金属(如Co、Ag)催化加速细菌氧化反应的速率,使金属阳离子取代矿物表面硫化矿晶格中原有的Cu2t、Fe³+等离子以增加硫化矿的导电性,从而加快了硫化矿的电化学氧化反应速率。
(4)用于水泥和建筑行业
炼铜炉渣水淬后是一种黑色、致密、坚硬、耐磨的玻璃相。密度为3.3~4.5g/cm³,孔隙率50%左右,细度3.37~4.52,属粗砂型渣。表6-19为铜渣在水泥工业及建筑行业的应用情况。
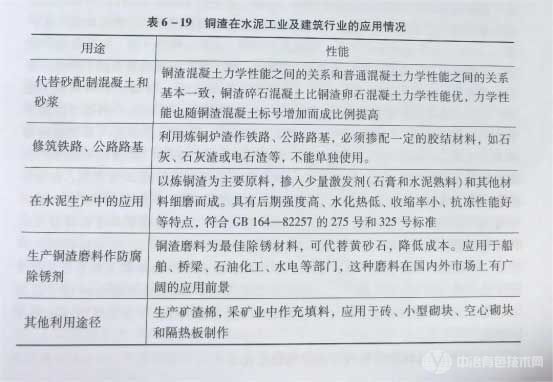
炉渣的选择性析出是利用炉渣的高温热能,通过合理控制温度、添加剂、液体的运动行为改变渣的组成和结构,从而实现渣中有价组分的回收和资源化,已成功应用于含钛高炉渣、硼铁矿等复杂矿物的处理。向含铜熔渣加入还原剂首先降低渣的黏度促进铜的沉降,待铜沉降到一定程度后使渣迅速氧化,提高磁性氧化铁的含量,缓冷粗化晶粒,磁选分离含铁组分,实现铜渣中残余铜的含量从5%降低到0.5%以下,渣中Fe,O4含量从26.8%提高到50%以上。
(6)铜冶炼高砷物料中砷的脱除与固化——稳定化技术
砷是伴生于铜精矿中且对铜冶炼过程及环境保护极其有害的元素。我国铜精矿行业标准(YS/T318—2007)将铜精矿分为5级,1级至5级铜精矿As含量分别限定为不大于0.1%、0.2%、0.2%、0.3%、0.4%。国家强制性标准《重金属精矿产品有害元素限额规范》规定,铜精矿中As含量不得大于0.5%。
近年来,由于优质铜资源减少,国内生产及国外进口铜精矿中砷含量均呈现上升趋势,根据有关铜冶炼厂报道数据估计,目前我国铜冶炼厂所用铜精矿,平均砷含量为0.25%。2013年,我国精炼铜产量达到663万t,其中矿产精炼铜产量约400万t。据此推算,我国随铜精矿进入铜冶炼系统的砷量达4.0万t/a。
砷在铜精矿中主要以硫化物形式存在,如硫砷铜矿、砷黝铜矿、黝铜矿、黝铜矿、含砷黄铁矿、砷黄铁矿、雄黄和雌黄等。在铜火法冶炼中,砷分散分布于烟尘、炉渣、铜锍或粗铜中,其行为与原料成分、冶炼工艺及技术条件等相关,十分复杂,但其最终出口主要有以下几处(以奥图泰闪速富氧熔炼为例):熔炼炉渣(电炉渣),占进入系统总砷量的30%,如果直接外销,这部分砷将开路,如果对电炉渣进一步选矿处理,这部分砷将大部分(约80%)随渣精矿返回熔炼系统;吹炼白烟尘,占进入系统总砷量的10%,在火法炼铜各类烟尘中,白烟尘含砷最高,达15%左右,且含有其他有价金属,因此大部分企业都将其单独或外销处理以便从系统中开路部分砷;熔炼和吹炼SO烟气净化污酸,所含砷量占进入系统总砷量的40%左右,一般企业将其硫化沉淀,得到硫化砷渣,再进一步湿法处理生产白砷产品或返回配料或外销;粗铜,所含砷占进入系统砷总量的20%左右,在电解精炼溶液净化中,砷大部分进入黑铜板或黑铜粉返回系统。随着铜精矿砷含量的升高,产生了两方面的问题:第一是系统中砷开路不足,形成累积导致硫酸及电解铜生产受到不利影响。一般是将含砷较高的物料,如白烟尘、黑铜粉和硫化砷渣等,从系统中开路出来,单独处理。国内外都有成熟的技术和工业实践,如美国肯尼科特公司Garfield炼铜厂、智利国家铜公司(Codelco)下属含砷烟尘处理厂、我国云南铜业公司等。第二是砷的安全环保处置问题,目前在我国还未能很好解决。
(7)铜冶炼高砷物料中砷的脱除与稳定化
在火法炼铜中,砷从废气、废水途径的排放,通过采用严格的环保控制措施,均能实现达标,目前至少技术上已无问题。存在的问题是随着优质铜资源的减少,复杂、低品位铜矿的开发,随铜精矿带入冶炼厂的砷量日益增大,而安全稳定的砷开路出口仅有电炉贫化后水淬熔炼渣,或熔炼及吹炼渣选矿尾矿,对多数炼铜厂而言,会造成砷开路不足而在系统中累积,影响生产、环保和卫生。前已述及,在铜资源日趋紧张的情况下,炉渣选矿已成为从铜冶炼渣中回收铜的主流技术,在我国得到普遍应用。在炉渣选矿的情况下,炉渣中的砷约80%进入渣精矿返回熔炼,选矿尾矿中仅能开路进入系统总砷量的约6%(30%×20%),这将使砷在系统内循环累积的问题更为凸显。因此,从硫化砷渣、高砷烟尘或黑铜粉等火法炼铜高砷物料中将砷脱除开路,然后将铜等有价金属回收返回系统,已成为发展趋势,目前在国内外很多原料含砷较高的炼铜厂,正是通过这一技术措施解决了砷累积的问题。仍存在的问题在于,砷属剧毒、致癌和“过剩”元素,冶炼回收的砷远远超过其应用所需,因此大部分的砷只能固化后堆存,而这一问题目前在我国仍未很好解决。
据美国地质调查局(USGS)报道,2011年全球主要砷生产国白砷(砒霜,As,O)产量为5.2万t,其中,我国是最大生产国,达2.5万t。据估算,我国随有色金属精矿或矿石进入冶炼系统的砷量,每年至少达到10万t以上,而随炉渣带走的量,估计只有约3万t,其余除少量随含砷废水净化渣带走外,大部分富集于各类高砷物料中,或在系统中循环累积,或转化成白砷产品,甚至还有部分流向中小企业,造成严重的安全与环境隐患,这也正是近年来我国砷污染事故频发的原因之一。
从铜冶炼高砷物料中脱除的砷,全部转化成白砷或金属砷产品,是没有销路和经济效益的,使其固化—稳定化后堆存是主要的方向。针对这一问题,国内外开展了大量研究,国外研究主要集中在加拿大、日本和智利等国的学术与产业界。国内近年来也有一些研究和实践。曾研究过使含砷物料与高温熔融炉渣混合,将砷固化在炉渣玻璃体中而实现稳定化,结果表明,在这高温过程中,砷化合物会大量挥发,由此也证明玻璃包封方案不可行。水泥包封固化是一种可行的方案,但其固砷产物量太大,成本过高,并未得到广泛采用。硫化砷、砷酸钙在堆存中与空气和水接触,均会发生分解而不能稳定固化砷。这种方法沉砷渣含砷低、含水高,只适用于含砷浓度相对较低的废水处理,而不适合于作为高砷物料中脱除砷的固化方案。
在水热或常温条件下,通过对结晶过饱和度的控制,均可使溶液中的As(V)和Fe(Ⅲ)以臭葱石沉淀。目前,智利国家铜公司已建成一家处理高砷铜烟尘的工厂,采用加拿大McGill大学Demopolos教授研发的分步控制过饱和度的方法,使砷从含Fe(Ⅲ)的浸出液中以臭葱石沉淀堆存,然后再从沉砷后液中采用萃取法回收铜、锌等有价金属,目前年处理高砷烟尘5~7万t。最近的研究也表明不同条件下沉淀的臭葱石,其稳定性相差甚大,这是值得进一步深入研究的问题。
我国是世界上最大的矿铜冶炼生产国。目前,仅有部分砷转化为白砷产品。对铜冶炼高砷物料中砷的脱除与固化—稳定化,虽然有一些研究,但在工业应用上还未起步,应引起重视并尽快付诸行动,为砷的减排和污染防治奠定坚实基础。